Alleviating the Risk from Above
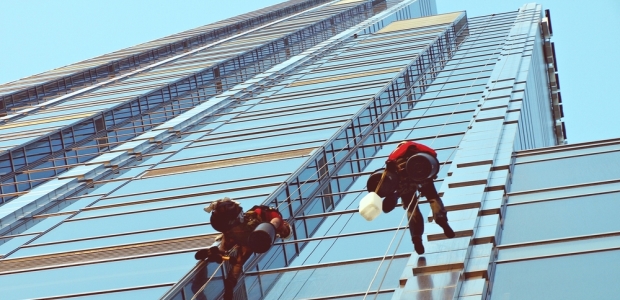
Head and face protection begins with hard hats. An OSHA enforcement action1 just two weeks into 2017 illustrates why it doesn’t end there. OSHA cited a Massachusetts auto parts company for more than a dozen serious violations and issued $27,157 in proposed penalties after an employee suffered fatal head injuries while trying to mount a multi-piece rim wheel on a vehicle in October 2016. The case involved much more than PPE alone—there were violations2 of training, personal protective equipment, electrical safety, exit route signage, powered industrial truck, and HazCom regulations, according to the agency’s Braintree, Mass., office.
Last year, the International Safety Equipment Association announced some of its member companies were at work on the first industry consensus standard establishing minimum design, performance, and labeling requirements for products that prevent dropped objects incidents in industrial and occupational settings. That’s significant because the Bureau of Labor Statistics reported 240 deaths in 2014 from being struck by a falling object or equipment, “which accounted for approximately five percent of all workplace fatalities,” the International Safety Equipment Association (ISEA) noted.
The 2016 Edition of the National Safety Council’s indispensable “Injury Facts” publication informs us that head and neck injuries accounted for 12 percent of the injury-related emergency department visits in 2011 in the United States, and that head/central nervous system injuries were the most costly workers’ compensation claims in 2012-2013. The average total costs incurred for them in that period were $78,183, more than double the average for all claims of $37,738, according to the 2016 Edition.
This fact book also shows how often falls to a lower level and same-level falls result in head injuries. There were 2,470 cases of head injuries from falls to a lower level in 2013 that resulted in lost time and 9,420 cases of same-level falls that year that caused days away from work.
Overall, it reports, there were 69,680 occupational head injuries involving days away from work in private industry during 2013, or 7.5 percent of the total private-sector nonfatal occupational injuries and illnesses involving days away from work that year. Construction head injuries accounted for 5,730 of those 69,680 injuries.
OSHA’s 29 CFR 1910 Subpart I, Personal Protective Equipment, contains sections about eye and face protection (1910.133) and head protection (1910.135). Section 1910.133 requires employers to ensure that all affected employees wear eye or face protection PPE when they are exposed to eye or face hazards from flying particles, molten metal, liquid chemicals, acids or caustic liquids, chemical gases or vapors, or potentially injurious light radiation. They also must ensure that each affected employee uses PPE that offers side protection when there is a hazard from flying objects. This section of the PPE regulations requires that eye and face PPE comply with ANSI/ISEA Z87.1, American National Standard for Occupational and Educational Personal Eye and Face Protection Devices; the current edition is ANSI/ISEA Z87.1-2015, which is available from ISEA, www.safetyequipment.org.
Dropped Object Prevention in Oil & Gas
Several U.S. fall protection manufacturers have been stressing the importance of preventing dropped-tool incidents and injuries in recent years and also introducing new products for this purpose, including lanyards, tool pouches, tool belts, and soft buckets to hold tools.
DROPS Global is a British organization that brings together oil and gas industry companies worldwide in a work group seeking to prevent dropped objects. “It’s not just about equipment damage and lost production,” the organization’s website explains. “It’s about life! The problem is common to everyone in the industry, across all regions, sectors, and disciplines.”
DROPS’ “Recommended Guidelines for the Safe Use of Tools & Equipment at Height”3document, issued in April 2011, contains recommendations for hand tools; power tools; tool storage; lanyards and tool attachment points; and tool bags, pouches, and belts.
Tools and portable equipment used at height should be properly secured to the user or the workplace, and “at height” tools should be used for tasks at 2 meters’ height or higher, or where there is a potential for tools to fall more than 2 meters, it says. Such tools should be lanyard-attached to the toolbag, to the worker’s harness, or the workplace itself, and they should be manufactured and supplied with tested and certified lanyard attachment points. The lanyard attachment point on the tool must still enable the tool to be used effectively, according to these guidelines.
References
1. https://www.osha.gov/pls/oshaweb/owadisp.show_document?p_table=NEWS_RELEASES&p_id=33699
2. https://www.dol.gov/sites/default/files/newsroom/newsreleases/OSHA201748.pdf
3. http://www.dropsonline.org/assets/documents/Recommended-Guidelines-for-Safe-Use-of-Tools-at-Height-April-2011.pdf